Fast-track repairs keep ball mills rolling
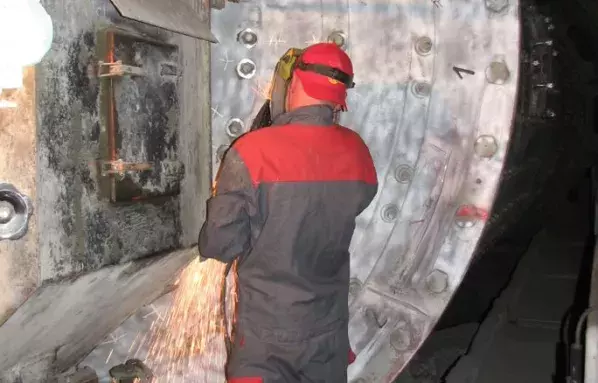
Cement plants often rely on original equipment manufacturers (OEMs) to deliver regular repairs and maintenance on ball mills. However, the task of breaking up clinker is extremely challenging and ball mills can experience unplanned outages due to excessive wear. Mathieu Castonguay, Workshop Services Manager Americas from Castolin Eutectic explains how to return them to service on a fast-track basis.
Ball mills can experience excessive wear on areas such as diaphragms, linings, and grinding media due to the abrasive and corrosive effects of cement particles as they are crushed. This wear significantly shortens the life of the components themselves. However, it will also reduce the energy efficiency of the ball mill. When components are worn, they are less effective at crushing cement, therefore require additional time and energy to achieve the same effect.
When premature wear occurred on a ball mill’s liner at a cement plant in Canada, the operations team called us in to make fast-track repairs in November 2021. The mill had experienced excessive wear on liners in the section closest to the entry. Cement in this first section is less broken down and therefore hits the liners with greater mechanical force, creating more abrasive conditions than in later sections.
The wear had triggered the operators to take the ball mill out of service and pause the plant’s cement production.
Ball mill liners are not standardized and therefore are not available to buy as off-the-shelf spares. They need to be specially cast from wear resistant material in the precise dimensions required for each mill. We evaluated the ball mill’s existing liners by taking detailed measurements. This enabled us to develop a plan to reverse engineer new liners from our standard CDP® (CastoDur Diamond Plates). These wear plates are based on composite bi-metallic materials.
Different types of wear plates are available, depending on the application. The choice of wear plate depends on the hardness and abrasiveness of the media being crushed in the industrial processing equipment.
In the case of the cement plant, our team selected a wear plate product suitable for withstanding the high pH and abrasive nature of cement. This was the most promising option, partly because of the good performance of wear plates in cement applications, but also because the wear plates were available in stock. Therefore, they offered the best opportunity of returning the ball mill to service quickly.
While the mill was out of service, the team also took the opportunity to refabricate an access door. In total, the team was able to cut and fabricate the liners and deliver the replacement access hatch in less than two weeks.
Replacement tooth for girth gear
Another fast-track repair was needed when an operator experienced fatigue cracking at the root of a girth gear on one of its two ball mills in October 2020.
Girth gears are the large gears that run around the exterior circumference of the ball mill. They provide mechanical leverage so that a motor can power the mill’s rotation. A cracked tooth is a major issue. Left unchecked, the crack would eventually propagate and cause the tooth to fail, preventing rotation of the mill and stopping production.
Ordering a new gear would require several months of lead time and logistics to forge and machine a component of this size and arrange for its delivery to the site. Replacing the gear in situ was the fastest and most effective option as the gear is integral to the body of the ball mill, therefore it was not possible to remove it and carry out repairs in the workshop.
With this in mind, the project scope was to remove the tooth, weld a replacement into place and shape it to the correct geometry.
This was a complex and delicate job as it was essential that the repaired tooth would have the same mechanical properties and precise dimensions as the original and all the other teeth in the gear. In addition, it’s vital to pay particular care when making a repair on a fatigued component as the heat of welding could potentially introduce additional stress into the material and lead to the propagation of other cracks.
Mechanical properties are affected by the choice of material and also by heat treatment that components experience in production. We selected a special alloy called Nucleotec 2222. To repair we cut and gouged off the old teeth and build up a new one with Nucleotec 2222. Then the gear was shaped with onsite grinding and machining, the next stage of the repair was to grind the new tooth to size.
The repair required almost 800 man hours in 10 days (2 teams or 3 persons working round the clock for 10 days) to put the ball mill back into operation, ensuring the operator had both ball mills available.
Ensuring continuity of production
The lesson with unplanned outages is that it pays to be prepared. However, if an operator does not have the required spare parts in stock, it is possible to carry out fast-track repairs, enabling a mill’s rapid return to service and ensuring continuity of production.